Services
SERVICES

Our film development services are best-in-class, with a global top market share in both protective films for polarizers and insulating films for electronic components. With our capacity to commercialize your products, we aim to exceed expectations.
At Zacros, we process over 300 prototypes a year.
Our ability to handle and convert unwieldy materials such as insulating resins and ultra-thin films of liquid crystal polymer (LCP) can greatly contribue to the successful development of your product.
This “one-stop-service” we offer spans from small-volume prototypes and process development to larger projects like commercial production and quality assurance.
Total Solution Provider
We are more than just a simple OEM: with what Zacros brings to the table in terms of production know how and technology, we can not only realize your product design but also propose improvements from start to finish, such as scalability, material selection, and more.
Global Presence
In Japan and Taiwan, we have both sales and coating operations with sufficient capacity and customer support to quickly process your requests. The Japan operation also has an extruder for forming materials into films. In China (Shenzhenand Shanghai) we have sales offices as well.
Track Record
Despite over 300 complicated, novel material development requests coming in yearly, our process engineers and technical team succeeds in overcoming and commercializing projects that other converters could not.
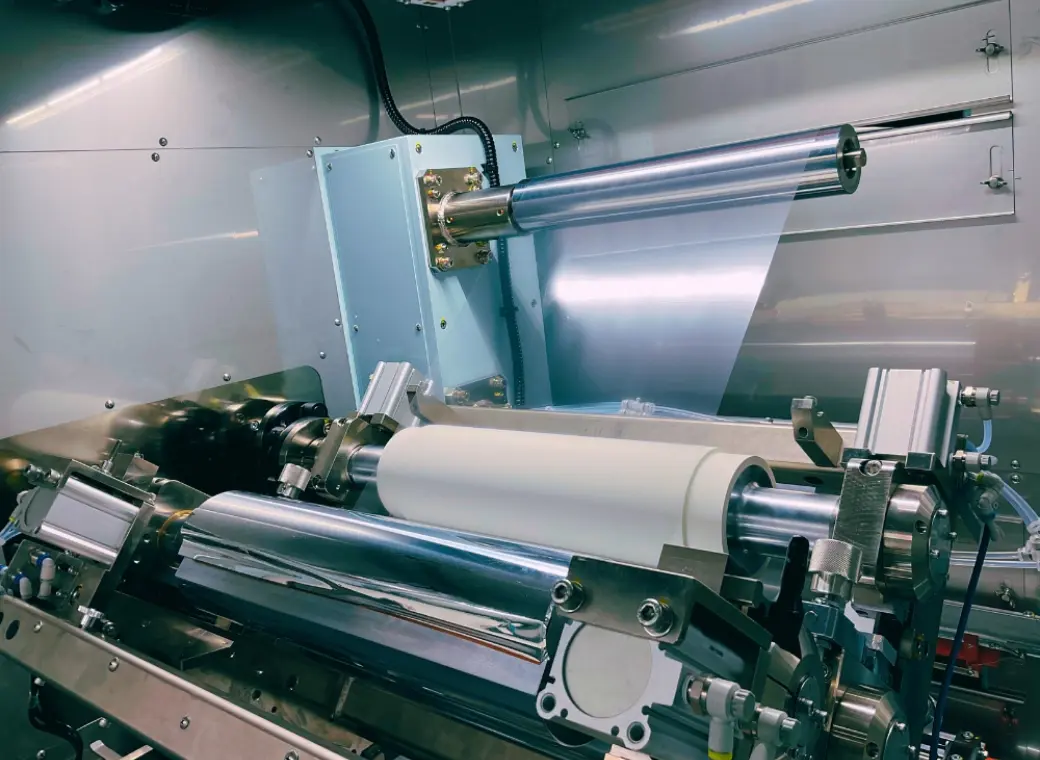
Coating Services
In the electronic components industry, even the smallest slip in quality leads to total product failure. Immaculate production environments, stringent quality management, and consistency is the only way to mitigate errors in quality.
Our coating know-how is best-in-class, with capability to precisely, consistently coat on ultra-thin and/or ultra-thick films.
Our technological contributions to customer product innovations are recognized domestically in Japan and abroad.
Coating Service Highlights
Industry leading track record in the development and manufacture of coating for insulating films and polarizer protective films
Consistency and accuracy in both ultra-thin and ultra-thick coatings
Capacity to apply a wide variety of materials, including both low and high viscosity applications
Prototyping of coating solutions from as little as a “cup-full”
Immaculate manufatcuring environment, with many of our products suitable for use in sensitive, precision equipment
Expanding global presence with manufacturing capacity established in Taiwan
Coating Specification
Coater | Coating width(mm) | Roll width(mm) | Film transport system | Class | Options |
---|---|---|---|---|---|
Lab (1/5 scale) |
50-550 | 600 | Roll supporting | ― | UV irradiation |
Medium | 500-1,400 | 1,500 | Roll supporting | 100(at coating process) | -Multilayer coating -Small-lot mass- production |
Large | 500-1,600 | 1,700 | Roll supporting or air floating | 100(at coating process) | -Double-sided simultaneous coating -UV irradiation |
Our coating services have the capacity to meet your needs, such as:
- Consultation and prototyping services to determine optimal film thickness
- Coating services with consistent thickness
- Suggestions for base film material
- Conversion of resin, or coating solution into film form
Coating Services Flow
-
01
Contact
Please fill out the contact form with as much information as possible, describing the desired end product, type of material/solution, thickness, etc.
The more information available, the faster we will be able to respond to the inquiry. -
02
Lab Prototype
By using hand coaters and scaled-down coating equipment we can rapidly iterate and develop the product.
-
03
Prototyping & Evaluation
After evaluating prototypes and identifying worthy candidates, we will ask you to evaluate those prototypes yourself. There are some cases when we can complete the evaluation on your behalf. Please refer to the equipment selection below. If everything is to spec, we will scale up operations to mass production.
-
04
Mass Production
With full scale production, clean rooms, process controls, and quality assurance come as a total package. Through our robust production environement we will deliver consistent quality, and through our wide sales network, we can also function as a sales force for your product on your behalf.
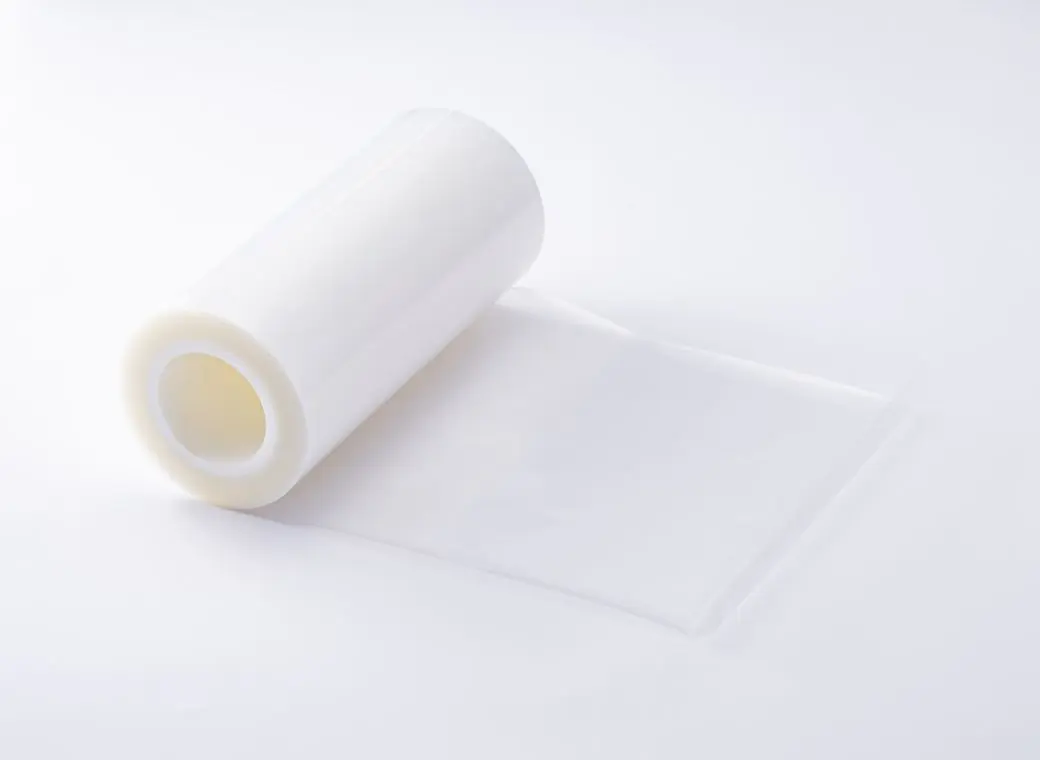
Extrusion Services
We can extrude your resins onto base films we supply, converting them into a multilayered film. With our extruder, we can co-extrude up to 3 kinds of resins at once, creating multilayer constructions up to 5 layers.
For any challenges in converting your resin into films, we will share our expertise in cast film forming and help overcome any challenge.
With extrusion, it’s possible!
5 layer film coextrusion with 3 different resins
Composite films by extruding onto base film then laminating an additonal material
Small-scale prototyping from very small quanities of resin is also possible.
Casting specification
Film forming system | Roll width(mm) | processed width(mm) | Resin thickness(μm) | Options |
---|---|---|---|---|
Extruder A | -3,000 | 800-2,800 | 20-150 | Simultaneous two-layer extrusion and lamination by the tandem-type roller. |
Extruder B | -1,750 | 800-1,550 | 20-150 | Manufacture of roll products with two layers of substrate and resin. |
Extruder C | -1,900 | 800-1,600 | 20-150 | -Corona discharge treatment facilities available -Dry lamination available(~1,500mm) |
Casting machine | -1,000 | 400-720 | 50-100 | -Simultaneous two-layer extrusion and lamination by the tandem-type roller. -Clean level: 10,000~(at manufacturing process) |
Our extrusion services have the capacity meet your needs, such as:
- Film conversion and/or film manufacturing of resin or coating solution
- Combination of multiple resins for a multi-functional film composite
- Proposals for base film and/or release liners
Extrusion Services Flow
-
01
Contact
Please fill out the contact form with as much information as possible, describing the desired end product, type of material/solution, thickness, etc.
The more information available, the faster we will be able to respond to the inquiry. -
02
Prototyping
Extrusion prototyping will be performed on commercial scale machines, so results and evaluations will be representative of actual products
-
03
Prototyping & Evaluation
After evaluating prototypes and identifying worthy candidates, we will ask you to evaluate those prototypes yourself. There are some cases when we can complete the evaluation on your behalf. Please refer to the equipment selection below. If everything is to spec, we will scale up operations to mass production.
-
04
Mass Production
With full scale production, clean rooms, process controls, and quality assurance come as a total package. Through our robust production environement we will deliver consistent quality, and through our wide sales network, we can also function as a sales force for your product on your behalf.
Optional Services
When placing coating or extrusion orders with us, we offer additional optional services for further processing of your product
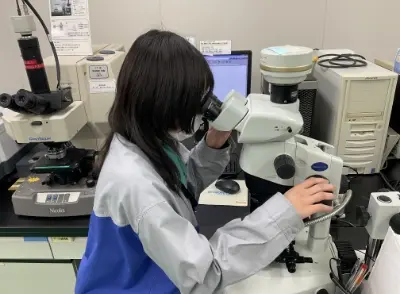
Analysis Services
With fast turnaround times, we offer a complete suite of analytical equipment to accelerate development of your materials
Observational services
- Microscope
- Confocal laser scanning microscopy
Pretreatment services
- Ion milling
- Micromanipulators
Principal Component Analysis services
- Fourier transform infrared spectroscopy
- Gas chromatography/mass spectroscopy (GC/MS)
- Fluorescent x-ray analysis device(XRF)
- Electron microscopy combined with energy-dispersive X-ray spectrometry (SEM-EDX)
- Wavelength dispersive X-ray fluorescence spectrometer
- Raman spectrophotometers
Physical Property Evaluation
- Differential scanning calorimetry(DSC)
- Differential thermal/thermogravimetric simultaneous measurement device(TG/DTA)
- Viscoelasticity measuring device
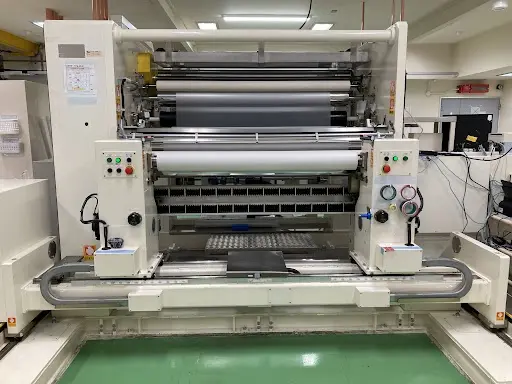
Lamination
By coating multiple different resins onto base films, various barrier and other strengths can be realized in a single composite film.
Machines | Roll width(mm) | Process-able widths (mm) | Maximum winding diameter (mm) | Range of thickness(μm) |
---|---|---|---|---|
1 | 3,000 | 800~2,800 | 1,200 | 20~150 |
2 | 1,900 | 800~1,550 | 1,000 | 20~150 |
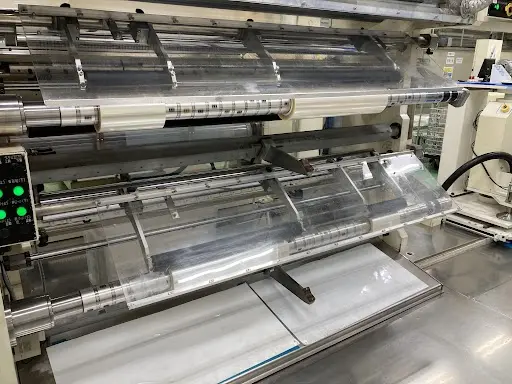
Downstream processes
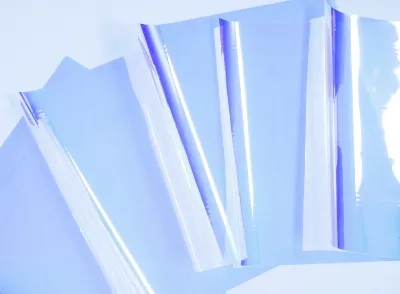
Slitting, rewinding (inspection)
Slitter | Rewinder | |
---|---|---|
Maximum width (mm) | 1,600 | 1,600 |
Maximum winding diameter (φ) | 500 | 1,000 |
Maximum load capacity (kg) | 20-580 | 800 |
Class | 10,000- | 10,000- |
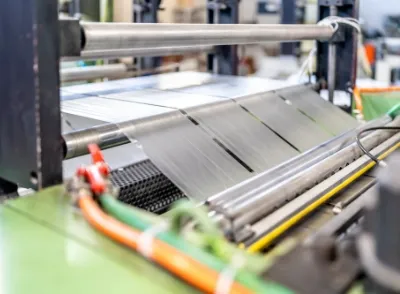
Cutting, punching out
Cutter | Puncher | ||
---|---|---|---|
Maximum width (mm) | 600 | Maximum area (mm) | 600×900 |
Maximum length (mm) | 900 | ||
Thickness (um) | 30~500 | ||
Tolerance | ±0.2mm~ |
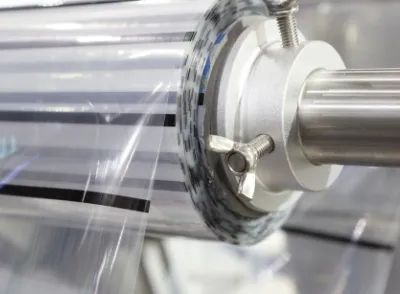
Annealing
Maximum size | 1,000×1,000×1,000 |
---|---|
Maximum temperature (℃) | 500 |
Annealing process | Per batch |
Atmosphere gas | Carbon dioxide gas |
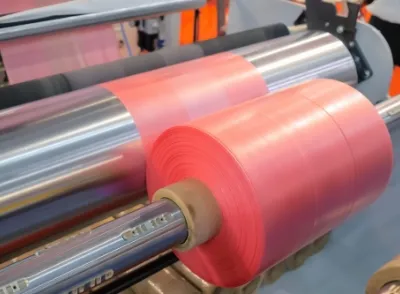
Printing
Contact
For inquiries, please contact us below